A Quickstart Guide to Standard Operating Procedures
Most of us have been in this situation - you just got hired and you want to do things right, but almost everyone you speak with has their own idea of the best way to get them done. In that context, many errors are made and much unnecessary and expensive rework is produced. Companies like this that don’t invest the resources to define a standardized way of doing things are often highly disorganized, with many pockets of individuals working inefficiently in disjointed silos. In contrast, companies that put in place processes and systems that foster collaboration are much more productive and effective, and much more likely to succeed.
In this article, we’re going to look at how you can establish a set of standard operating procedures (SOPs) to help ensure everyone in your company is working from the same page. We’ll explore what SOPs are, how they differ from process documents, and why they’re so important in day-to-day business. We'll then review the different types of SOPs and discuss what makes one set better than another. After that, we’ll learn about some of the most common challenges encountered in creating SOPs, and finally, we’ll walk you step by step on how to write and deploy effective SOPs for your own business.
What exactly is an S-O-P?
In short, a Standard Operating Procedure is a document that lays out a set of precise directions guiding the correct completion of a routine task. You may be thinking to yourself, ‘I know my business better than anyone - why would I need this?’ Well if you’re an operator with just one or two employees and no plans to scale, your time may be best spent elsewhere, but the majority of business owners are growth-focused and can leverage the power of SOPs to help ensure their people and processes are running at maximum efficiency, with quality output and consistent performance.
SOPs are also excellent resources for onboarding new employees in record time and are often mandated by law to help ensure businesses are compliant with government regulations.
Process vs Procedure
It’s easy to get confused between procedural documents and those that define a process. The simplest way to envision one versus the other is to think of a process as the ‘what’ in a project, and SOP as the ‘how’. The process is the sequential flow of activities that define, in general, what needs to be completed, while SOPs are a highly detailed breakdown that lay out, end to end, each individual activity.
For example, in construction, the seven-step process to construct a foundation is as follows:
In contrast to the above list, an SOP would break out each individual step in substantial detail. In this example, an entire SOP would be dedicated to excavation, and another to footings, and another to walls, and so on. Each SOP would go on to describe every element involved from set-up to takedown, listing out the materials and equipment to be used, in what order, by whom, and with what timings, including discussion on safety gear, considerations, communications protocols, deadlines, and so on. Often, SOPs include checklists, illustrations, photos, and even videos for added clarity.
In summary, process documentation gives stakeholders a high-level overview of the task to be completed, while SOPs deliver a step-by-step explanation of everything that needs to happen to ensure each step of the process is completed as expected, with the same results, again and again.
Another important thing to keep in mind is that while many SOPs are heavily detailed, they can also be as light or simple as needed. The key is having the right quantity of quality information to get the job done properly.
Why are SOPs so important?
Stimulate Productive Workflows
SOPs give businesses a tool with which they can develop an instructive framework around their processes, ensuring everyone involved is thinking on the same lines, in turn stimulating effective, collaborative progression.
These documents give owners the power to establish a document structure within their company to ensure workers are following best practices, which can help minimize the risk of injuries or property damage, and can also reduce the likelihood of the company being sued for any number of reasons. When a mandate is imposed requiring that workers follow official procedures, the company can do business in a professional and productive manner. The alternative leaves too much to chance.
Foster Consistent Results
Another major benefit of SOPs is that they drive consistent results in an efficient manner. Once a procedure has been put in place for a specific process, you can run it again and again, safe in the knowledge that resources are being well provisioned and that a superior product is being produced each and every time.
Take for example a commercial bakery producing pies for a major brand. It’s imperative that every single pie has consistent size, flavor, texture, and appearance, and to achieve that end, the ingredients, mixers, and ovens must be used in exactly the same way, batch after batch. The only way to maintain this high level of consistency, other than using robots, is to put in place a mandatory standard operating procedure.
Consistency in procedures can also directly impact revenue. Customers who regularly receive the same high level of service or products are inherently more loyal and will happily return again and again.
Minimize Risks
In the event that there are questions on how to proceed in a task, SOPs provide a clear path forward. They can function as a guide to how things should be done and they layout potential risks to be avoided.
Imagine a new worker with a cleaning company who needs to deal with a stubborn stain. In the absence of SOPs, he might decide that mixing vinegar and bleach could work well, unaware that the combination would create noxious, potentially harmful vapors. An SOP in this situation would clearly lay out what chemicals should be used in what circumstances, and which chemicals should never be combined.
SOPs improve the likelihood of positive outcomes.
Enhance Proper Onboarding and Training
Every successful company is eventually faced with the need to bring on new hires, cross-train existing employees, adopt new technology, or establish new practices - and in all these cases, training is needed to get people up to speed.
When you take the time to break out each of your processes into their respective elements and then layer-on standard operating procedures, you will greatly improve the knowledge onboarding process. People will learn faster and more consistently, and best practices will be brought to bear across the board. Moreover, those with lingering questions or doubts will know exactly where they can find answers.
Improve Process and Reduce Inefficiencies
In establishing your SOPs, you will inherently identify all sorts of challenges and opportunities in the way things are currently being done. You will find many situations that can be improved and many efficiencies that can be added to reduce waste. As an added benefit, you will likely identify contingent circumstances that will need to have additional procedures built out - further enhancing your business flow.
Improve Operational Flow
In the absence of SOPs, there is an increased likelihood of operational blockages and bottlenecks. Drag from just one individual working inefficiently can negatively affect organizational efficiency across the board. Effective service delivery requires, at a minimum, that every employee is on the same page, and this is where SOPs really show their value. Formalized procedures that inherently ensure everyone is working in collaboration altogether eliminate the risk of any individual’s drag affecting the larger group.
SOPs are also great for resource management, offering a means of ensuring maintenance is completed on schedule and that major incidents are minimized and/or managed correctly to reduce operational impacts.
A good example of this might be a construction project leveraging a tower crane whose lifting cable has begun to fray - it’s a relatively common thing; wire rope fails for all sorts of reasons, but the single most predominant factor is lack of proper maintenance. When mandated as a regular part of daily work, SOPs can ensure that regular inspections take place and that proper maintenance gets taken care of, before accidents can occur.
Reduce the Risk of Panicked Action
In the face of an emergency, people tend to panic and make poor decisions which can easily make a manageable situation unmanageable. For example, a security guard at a chemical plant should know exactly what to do in the case that she smells smoke. Inaction or flawed action could be disastrous. For each potential situation, an SOP should be constructed that details exactly what steps should be taken, who should be contacted, what safety gear should be worn, etc.
What are the Different Kinds of SOPs?
Most companies use one of three basic templates when building their SOPs, each of which has inherent pros and cons. Which format you decide to use depends largely on your reason for creating the SOP in the first place, and on the complexity involved.
Ordered (Simple) CheckList
When faced with a clear, straightforward process that has few steps and/or that you are reasonably confident will function properly, again and again, the checklist method can work well. For example:
A major benefit of this approach is that checklists allow you to precisely monitor completion which is useful in assessing employee productivity. Also, because of the simplicity with which each step is ordered and completed, it is an excellent solution for instructions that require steps to be completed one after the other. Here's an example of a simple checklist for a security officer to ensure a facility is properly locked-up.
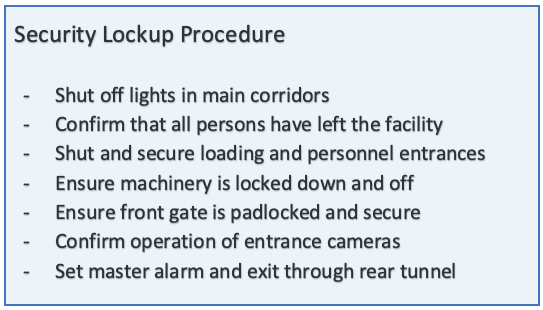
A related format that is better suited to detailed tasks is the hierarchical (detailed) checklist which looks the same but outlines main tasks in addition to subtasks.
Hierarchal (detailed)
When faced with a need to produce a list with additional detailed sub-task instructions, the hierarchical format is the way to go. While a normal, sequential checklist lays out A then B then C in an easy-to-follow routine, the hierarchical format might have A then A1 then A2, then B, and so on. It provides extra detail where a single task instruction is insufficient.
Take a look at this example; four basic tasks are broken down into their respective sub-tasks.
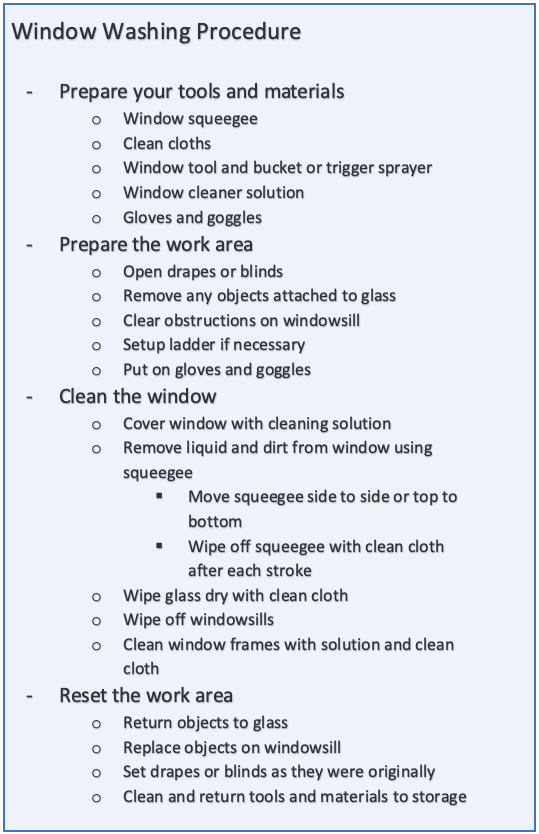
If the process is getting confusing, it may be a good idea to lay it out on a flowchart.
Flowchart
When dealing with a complicated process with multiple different outcomes, each outcome can radically change the downstream actions of the team. The best format to present this kind of process is the flowchart which lays out each step in an easy-to-understand visual flow. Flowcharts can help convert large and complex decision-making flows into simple, logical options.
Flowcharts use shapes and pointers laid out on a sheet to describe actions and deliverables. While much more difficult to lay out than checklists, once complete, they are much more easily and rapidly understood. One of the great values of flowcharts is they make it easy to assess where complications might arise and allow you to easily test new flows.
In addition to laying out process flows, flowcharts are commonly used to show organizational hierarchy, demonstrating who reports to who. Here's an example of a simple flowchart. Of course, they often get much more detailed and complicated.
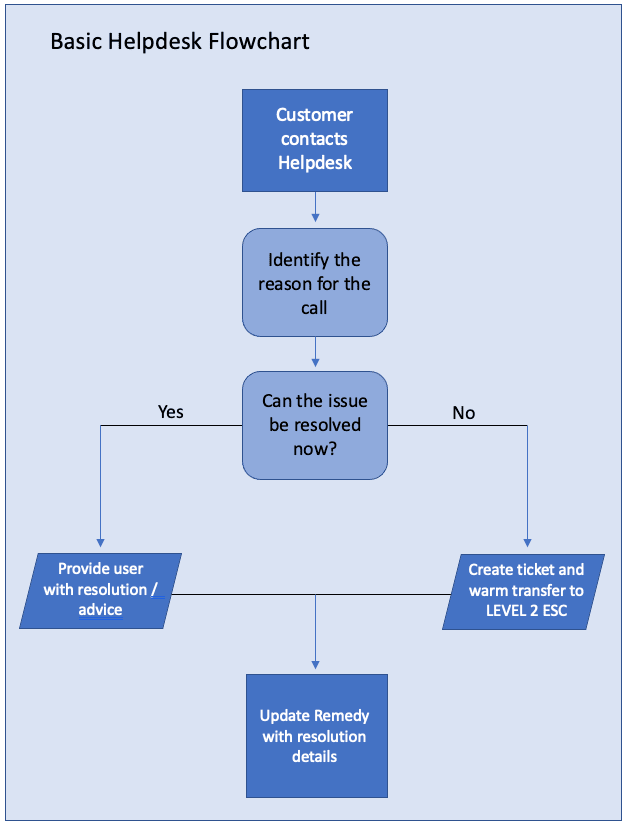
What are some challenges when creating SOPS?
There’s no doubt that SOPs offer a great number of benefits to any business, but at the same time, there are a fair number of potential challenges.
Developing SOPs in a Silo
Imagine asking the marketing director of a major beverage brand to write an SOP for the workings of labelling machinery on their bottling line. They may own the brand concept but they'd be lost on the technical specifications of the machinery because it's not their responsibility; another department would have that information. The same is true of processes that exist within the same department but at different responsibility levels - for example a team leader versus an executive vice president in the same business unit. The team lead can lay out the nitty gritty whereas the executive is better suited to strategy and vision.
No single group of people has all the answers. The best way of ensuring your SOPs exactly match your true processes and procedures is by including people from all teams, and all levels in the SOP development process.
Failure to Hear from Your Entire Team
When we first established our SOPs, years ago, we had confidently laid out our processes on the wall in the conference room and were mortified when a team member walked in and said, “Oh no no - we don’t do that anymore!” Needless to say, that was the day we began involving everyone in our process development and improvement.
You may think you know best how your employees are doing their jobs but the reality is that when workers are confronted with difficulties in their day to day workflows, they often put into place workarounds that, while functional, can be far removed from the business rules, and in some cases, may have negative, unintended consequences. Moreover, since workarounds seldom get reported back to the process improvement team, KPI performance is assessed and decisions are potentially made, all based on flawed data.
This is also why it’s so important to involve every level of the business in the SOP development process. Run focus groups at the department level; walk them through the process flow from end to end and ask them for feedback on specific tasks. Assess their knowledge of the business; you may find that there are some training opportunities to roll out in addition to the SOPs. Determine how they handle challenges, and what they do when faced with a situation that contravenes the current process. This will help you put in place systems to capture problems with the future SOP and ensure people aren’t circumventing the procedures with their own workarounds but are instead giving feedback to their leaders which is ultimately used to improve the SOP. It’s generally a good idea to include frontline workers in all process improvement initiatives. You want them to be confident in using and following the procedures and you want them to feel supported.
Failure to Keep SOPs up to Date
Many companies spend a significant amount of time building their SOPs and then drop them in a drawer and forget about them. The problem with that is that nothing ever stays the same; new technology, new materials, and new ways of working are constantly being invented, and the last thing you want is inefficiencies or worse from workers running the wrong processes, or the right processes in the wrong way.
If you’re going to bother investing the time (and therefore money) to build accurate SOPs, it’s not that much of a stretch to establish an SOP maintenance schedule to ensure your documents include the latest revisions.
Insufficient Materials, Equipment and/or Training
It’s imperative that team members have the training and resources to implement the procedures as they have been laid out in the SOPs, and that they are made aware of any procedural changes that affect their jobs.
Imagine the SOP for a janitor to strip the floor in a gymnasium. It may look like so:
If management decided to purchase an electric scrubber to speed up the stripping process, several steps would change. From a personnel perspective, training would need to explain the functioning of the new equipment, energy would need to be provisioned to make it function, and most significantly, scrubbing, neutralizing, and vacuuming would be completed at the same time - eliminating both time and resource cost. In the absence of SOPs, untrained cleaning staff may not realize that neutralizing and vacuuming were no longer needed. By ensuring SOPs are up to date, and that staff has read and acknowledged changes, you can rest assured that your business is running smoothly.
Lack of SOP Visibility and Access
You can imagine SOPs as living documents that are only as powerful as the people who use them. Procedural documentation is most effective when it is easily accessed by the team. All of your people need to have open access to the SOPs that relate to their roles, and there needs to be some sort of mechanism in place that ensures people are regularly engaging with the documentation and that questions and comments can be made and responded to.
SOPs should be maintained in a centralized database that ensures everyone across your company is looking at exactly the same, live information. The last thing you want is multiple copies of an SOP file circulating around the company with various revisions and updates - it will quickly become unmanageable.
What is the best way to write an SOP?
There is no established standard for SOPs and different people have their own preferences in style and content. Following are the steps we used when creating our own SOPs.
Establish Your Objectives and Vision
The first step before anything else is to define the reason you want to build SOPs in the first place. Book a conference room and get together with your leadership team and think about how exactly SOPs are going to improve your business. Make a list of some of the major pain points you’ve been experiencing that you think SOPs will help solve. Will they help improve productivity? Will they help improve the customer experience and other related metrics like client satisfaction and loyalty? Will they help eliminate waste? Will SOPs improve the bottom line?
Once you’ve identified the major challenges, you need to define the objectives of each SOP. This will help you, as you build the document, to ensure you’re staying in scope and that the procedures you’re putting in place are directly driving positive outcomes both in the immediate and long-term future.
Now is also the right time to assess whether you even need SOPs for certain processes. For example, when a worker starts their shift, they may be required to clock in - but does that process really need an SOP? There are many similar tasks people do all the time that are clear or intuitive and that won’t be improved with a set of SOPs. On the other hand, any task that is potentially confusing or that may require a step-by-step progression - such as the mixing of chemicals, is going to need some sort of guide to ensure workers are doing the task correctly again and again.
Define Process Users and Stakeholders
Next up, you should identify who is going to be the end-user of each SOP so that you can tailor the style and language specifically for that demographic. For example, the lexicon you might use with a senior executive may be different from that of a secretary. Moreover, the jargon surrounding trades roles may not be known to more senior positions. Make sure you’re writing your SOPs in the simplest way possible to avoid any confusion on your intentions.
When available, try to use imagery to both grasp the user’s attention and to ensure quick comprehension.
It’s also a good idea to be sure to involve everyone in the development of the SOP who may be affected by it - that means not just the end-users who can differentiate between the validity of individual processes, but also mid-level management whose role it is to establish best practices and create operational plans, to the executive level who deal mainly in strategy and long-term objectives.
Another important element is defining just who exactly is going to write the SOP documentation. Whoever it is that does it must have a solid grasp on the topic, and the ability to write plainly and logically.
Choose a Simple to Grasp Format
One of the most important elements of SOPs is the format you choose to write them in. Given that the objective of an SOP is to socialize the right way to do something, it is imperative that each element be simple to grasp and easy to comprehend. You should be able to pick up an SOP and instantly understand what it is you need to do. SOPs that are jumbled or otherwise disorganized, are counterproductive.
Earlier in this article, we reviewed the different format types in detail. To summarize, the three most commonly used are:
Simple Checklist: for extremely simple instructions Hierarchical (Detailed): for lists with multiple levels Flowchart: for complicated lists with split decisions
Of course, you should choose whichever format lays out the procedure in the simplest way. It never makes sense to complicate things unnecessarily.
Establish Your Scope
It could be that you’re building an SOP detailing how employees should set their login passwords - in such a case, a simple checklist would be fine. However, you may be developing an SOP that details an entire supply chain system as it snakes through departments and business locations. In such a situation, it would be necessary to work with multiple people in different business areas; a potentially time-consuming and complicated project.
Different procedures will have different levels of complexity. Some may reference other SOP documents, and yet others may include references to many different interconnected systems. By taking the time up front to set your scope, your document will be that much more pertinent, organized, and effective, and you’ll save a mountain of potential rework down the road.
As a final step, you’ll want to get stakeholder sign-off. You can help ensure your teams are on board by asking for their ‘stamp of approval' on the draft document before it goes to the printer.
Distribution and Followup
Now that you’ve created your SOP, it’s time to get it out to your team and ensure that it’s being used as you intended. First off, you’ll want to ensure all the relevant people have received the new document and have read through it. A good way to do that is by getting each person to ‘sign-off’.
Next, you’ll need to find a way to assess understanding of the new procedures; it’s one thing to have people read them and another to have them understood. Any process element that is not crystal clear at the outset (or that doesn’t make sense) will have a low likelihood of adoption. You will also need to identify knowledge gaps and if necessary, implement training.
Remember that anytime you make a change to the way you’re doing things you will need to update the SOPs. This could mean new equipment, new software, new policies or products, new materials or locations, etc. In fact, you may want to establish a role in the company to be in charge of ensuring SOPs are accurate, up to date, and that they’re being used effectively by the team. In larger companies, it may even be a dedicated position.
Finally, you can decide to write your own SOPs or you can farm the work out to third-party firms dedicated to the task; whichever you choose, you’ll still need to implement some process to ensure your new SOPs are being adopted, used, and updated regularly. Heck, maybe you should write an SOP for your SOPs!
Last Words
In conclusion, standard operating procedures can mean the difference between a productive, organized, and forward-moving company and one that stagnates. SOPs will help ensure your entire team is aligned, in focus, and working together on common objectives.
They can be used to improve onboarding, enhance safety, identify improvement opportunities, reduce waste, and share best practices. No matter what happens in the company; no matter who is absent, if you have SOPs in place, you can rest assured that even the most difficult tasks are being managed effectively and consistently.